By bringing colour model making in-house, German design studio Thinkable Studio has added a new element to its concept work that has helped it arrive at the best design faster.
Based in the southwest of Germany, Thinkable Studio’s focus is on consumer goods, industrial technology, and medical markets.
For its recent AR bike helmet project, the team quickly took its 3D designs into KeyShot and produced different colour and material renders, before taking these through to their Stratasys J55 3D printer, which then 3D printed a scale model of the designs.
Once the concept ideas had been honed down, a full-size prototype helmet and all its components could be produced in-house.
The concept accommodates the most complex AR technology within the bicycle helmet and transparent visor, and incorporates indicator lights and striking design textures.
Using the J55 3D printer and VeroClear material, the team were able 3D print a lifelike visor with integrated LED lighting. According to Thinkable Studio founder Jörg Schlieffers, without this 3D printing capability they would have never been able to match a 3D model to look like the intended design render.
“Having had experience with single-material 3D printing technologies, I knew this was the technology we needed to take our product design process to the next level,” he said.
The Keyshot renders of the helmet
“We are now able introduce CMF models much earlier in the design process compared to traditional methods and produce ultra-realistic prototypes that are pretty much identical to the final product.
Schlieffers explained that the project clients were left “blown away” by the models helping them meet customer demands and reach design verification earlier in the project.
“The results we achieve with KeyShot are fantastic,” continues Schlieffers. “It enables us to select textures for our designs, and generally speed up our design process significantly. In terms of software, it is comparatively better than anything that I have tried before.”
By bringing model making in-house, Thinkable Studio has reduced both costs and time for the prototyping process, while keeping all its product data in-house.
“With the J55, we have slashed the time it takes to create ultra-realistic models from two weeks to just one or two days and reduced our costs by up to 75 per cent,” he continues.
“These are exceptional savings that make a huge difference to the performance of our business and the speed with which we can meet client needs.”
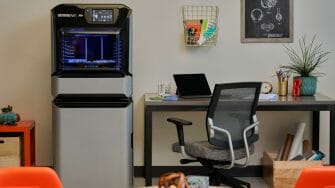